Right Substrate for Right Research
- Cecil Cherian
- Jun 17, 2020
- 4 min read
The most basic function of a substrate is to provide mechanical strength to the deposited thin films with proper adhesion and to act as a template for atomic ordering. However, with the development of material science, substrate selection has become a very critical factor in fine tuning the final performance parameters of thin films (Philips J.M., 1995). A substrate can be chosen to deliberately introduce chemical reactions between itself and the thin film, resulting in interdiffusion or it can be chosen to introduce strain in the film by increasing the lattice mismatch between the substrate and thin film. Mismatch between the thermal expansion rate is another factor which will affect the performance of the final thin film. For the purpose of developing a super hard biocompatible thin film, the substrate would need to have higher hardness value while retaining very high biocompatibility.
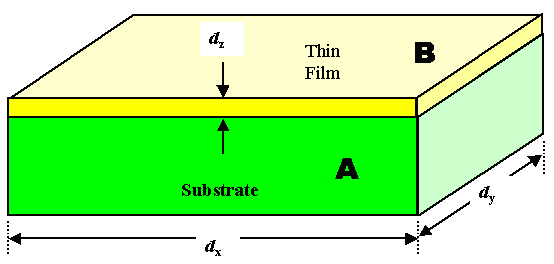
Deposition technique will have an influence on the type of substrate to be used. For example electroplating can only be performed on conducting substrates whereas thermal oxidation and other forms of chemical vapour deposition techniques require substrates to tolerate high temperatures. Characterization techniques also influence the type of substrates to be used. For cross sectional analysis using a scanning electron microscope (SEM) it is suitable to have a substrate which can be easily broken without disturbing the film. For structural analysis using X-Ray Diffraction (XRD) it is preferred to have an amorphous substrate or a substrate with a well-known diffraction pattern so that the substrate patterns can be subtracted to get better understanding of the film alone. For surface analysis using probing techniques such as atomic force microscopy (AFM), it is suitable to have a smooth surface finish to the substrate so that film features can be imaged and studied better.
The list of potential substrates for thin film deposition is vast. Soda lime glass is the most commonly used transparent substrate for thin film depositions. It is very easy to clean and with a melting temperature in excess of 1000ºC, can withstand higher temperatures encountered during sputter deposition of metals. With its high hardness value 6-7 on the MOH scale (for reference Ti is 6) and elastic modulus of 72 GPa, glass can be used for hardness measurement of thin films deposited on its surface. The smooth surface of glass is ideal for surface imaging, AFM probing and cross section analysis, while its amorphous nature makes it ideal for XRD studies of thin films deposited over it. Standard microscopic slides are very cheap compared to other substrate materials which makes them even more interesting to researchers. The main disadvantage of soda lime glass that although it is mainly composed of SiO2, it also contains detectable amounts of oxides of Ca, Mg, Na, K, S Fe etc, which can interfere with chemical analysis of thin films through Energy Dispersive X-ray spectroscopy (EDX). However, this can be easily overcome by depositing thicker layers of thin film such that the electron beam doesn't interfere with substrate. Borosilicate glass is an improved version of soda lime glass with significantly less impurities and better mechanical and thermal expansion properties. Quartz is pure version of glass with no impurities and is much more suited for high temperature applications with good resistance to thermal shock and is chemically less reactive. Then comes sapphire, which is an oxide of aluminium (Al2O3) and is best in its class with melting temperature up to 2000ºC and is used in the manufacture of scratch resistant surfaces. Most of the glasses are considered to be biocompatible because of their amorphous, chemically non-reactive nature.

With the advance in material science, devices made from metals were considered for long term implant within human body. Many grades of steel were considered for the medical grade application because of their non corrosive nature. 304, 316 L (low carbon content) and 316LVM (Low carbon content, vacuum melt) have very high hardness (1.9 – 2.2 GPa) and were suitable for surgical application. However, because of their very high elastic modulus (183-197 GPa) when compared to bone (30GPa) , they resulted in poor bone formation from stress shielding effect (more on stress shielding effect:https://www.hindawi.com/journals/ijbm/2011/836587/). Titanium (Ti) and its alloys are well known for their low toxicity, non-carcinogenic nature and extremely good biocompatibility. Ti grade 5 or Ti6Al4V is a medical grade alloy of Ti used in the fabrication of hip and knee implants because of its extremely good mechanical properties combined with biocompatibility. On a comparison scale, pure Ti stands at 1.2 GPa, slightly lower than medical grade steel, but medical grade Ti alloy of Ti6Al4V has a hardness value of 3.2GPa, which is higher than steel. On the contrary, the elastic modulus value of Ti and grade 5 Ti alloy is in the range 116-105 GPa, which is much lower than that of medical grade steel, making them better candidate for long term medical implants. Ceramics are other forms of materials used for fabrication of artificial implants. Most prominent among them is Oxinium (trade name of Smith and Nephew), an oxide of Zirconium, which registers a hardness value of 15-20GPa with an elastic modulus value in the range of 101-134 GPa, making it another industry favourite.
In order to develop a super hard and biocompatible thin film coating from β Ti3Au, two types of substrate were selected: soda lime glass 75 by 25 by 1 mm and mirror polished Ti6Al4V of 25 by 19 by 1 mm. Soda lime glass was chosen for its excellent balance of cost and it`s suitability with all of the intended characterization techniques. Whereas, Ti6Al4V substrate will help to recreate a real-life application of these thin films as it is already an established material for artificial joint fabrication. Also, Ti6Al4V is expected to have a better match with the Ti based thin film deposited on top of it, in structural, mechanical, chemical and thermal expansion terms, providing better film morphology, stability and adhesion.
If you are interested to know how the raw substrates are prepared before thin-film deposition please subscribe and read next article….
Comments